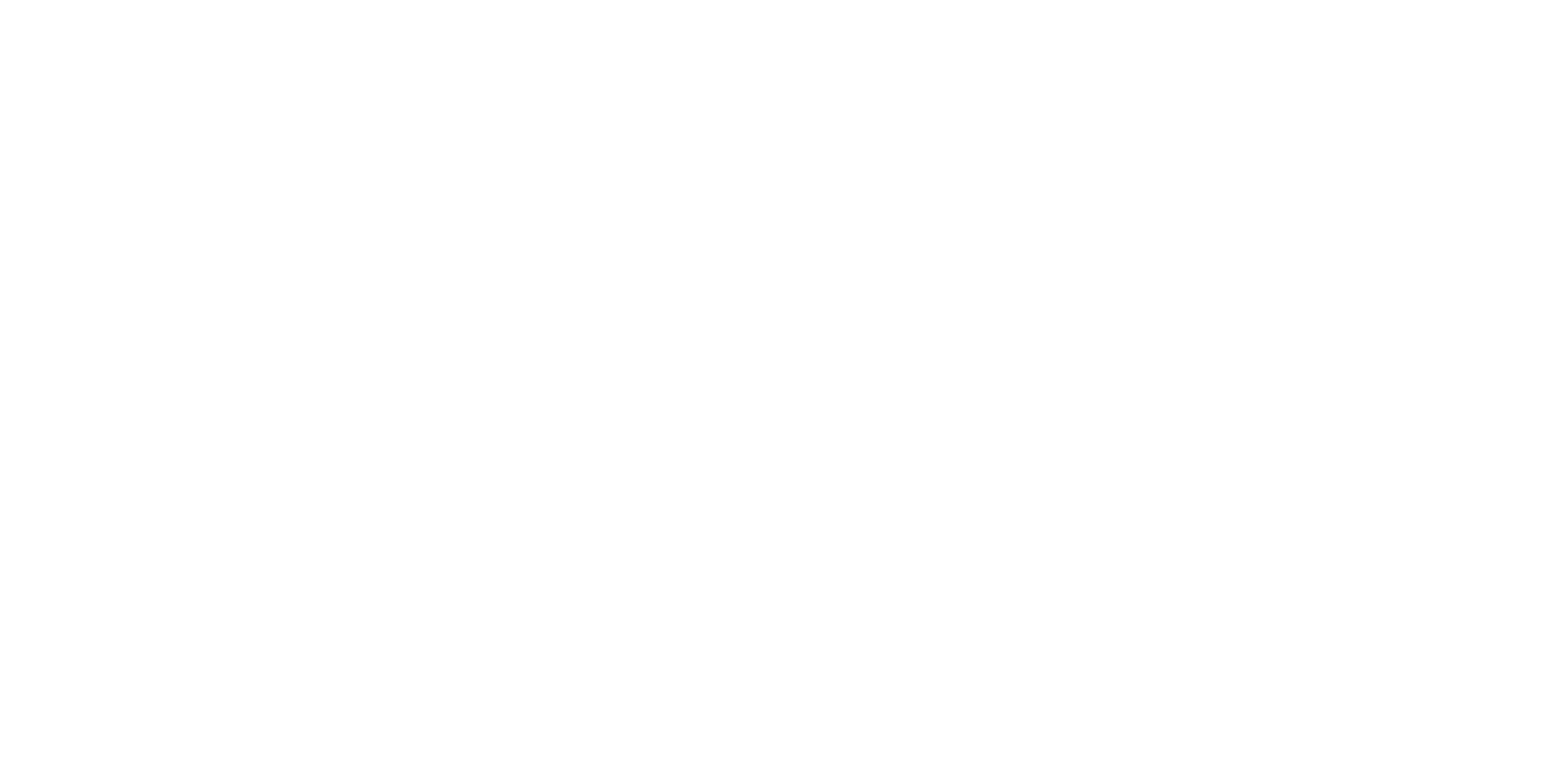
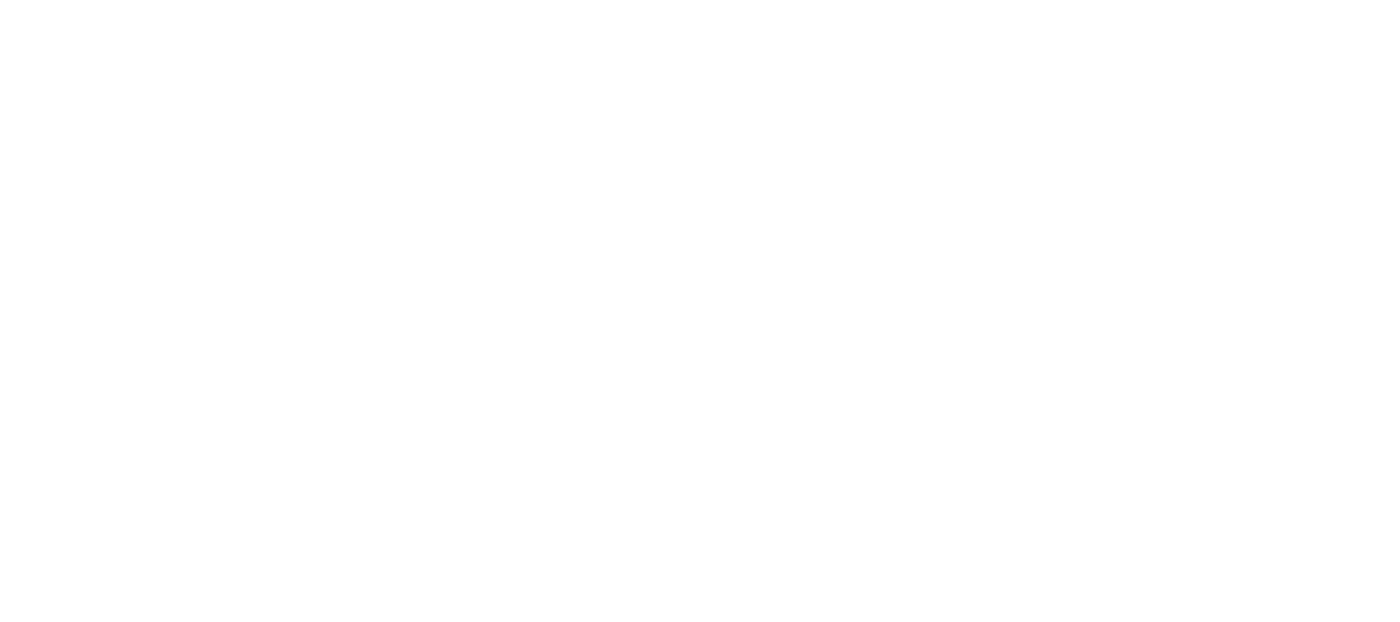

BPM as an Enabler of QMS Digital Transformation in GxP Regulated Industries
Please Select contact form.
Driving Compliance, Efficiency, and Innovation Through Process Automation
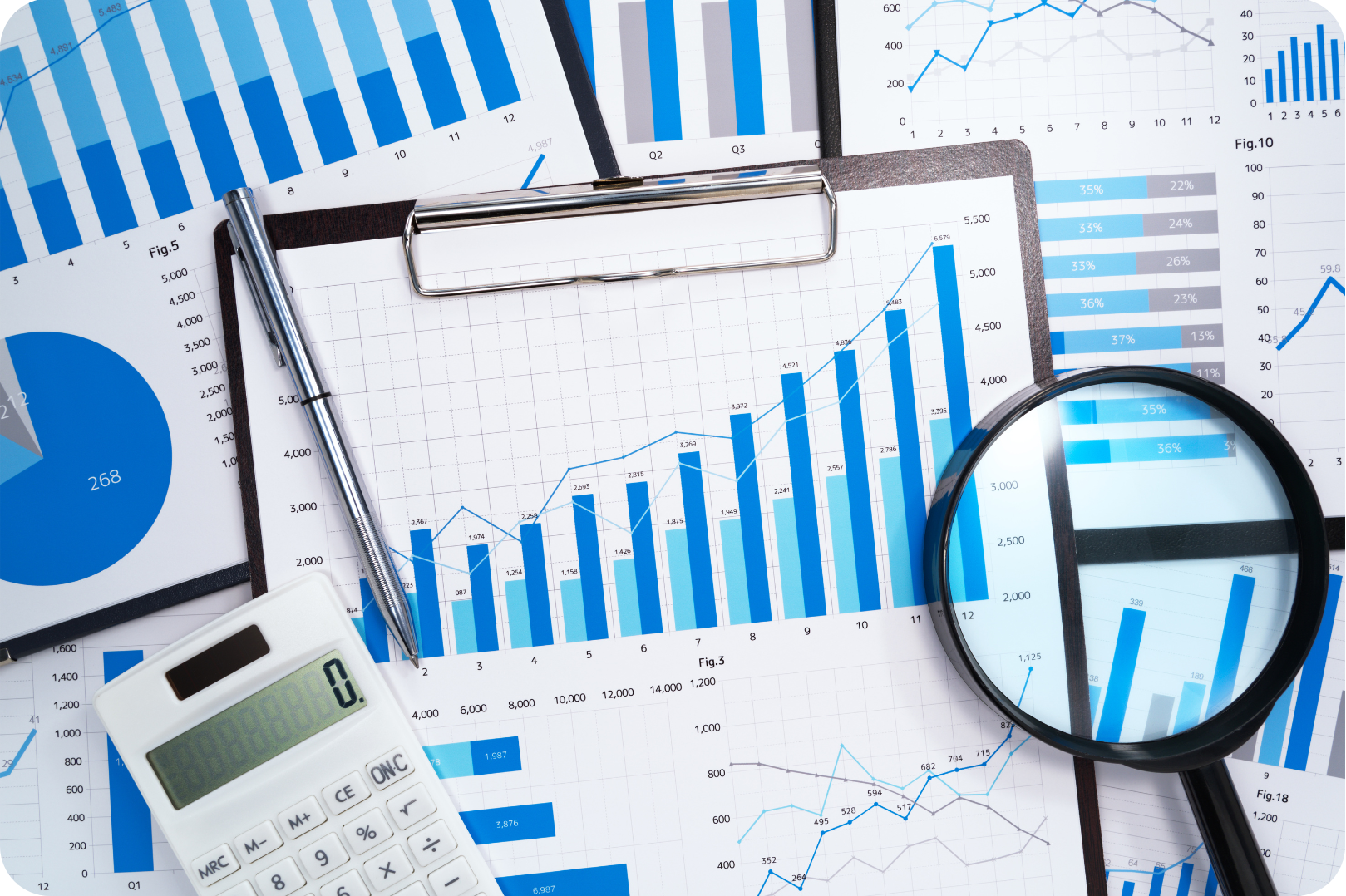
Summary
While Business Process Management (BPM) has proven to be extremely useful for various use cases in many industries and functions over the decades, it is still mostly unused in the GxP regulated industry’s core processes. This article summarizes the traditional elements of quality management systems. The conclusion is that these systems are not digitizable within the grown frame. The methods and tools of BPM, on the other hand, can be used to develop transformation routes.
Introduction
In a simple definition, a ‘regulated industry’ is closely monitored by government agencies. In this sense, many industries (not to say all) are ‘regulated.’ Obvious examples are financial services, aircraft and airports, and the pharmaceutical industry. From the company’s point of view, regulations are closely related to the so-called ‘license to operate’: ‘no compliance’ means no authorization to provide services or produce goods.
GxP summarizes all guidelines for ‘good working practice.’ The ‘G’ stands for ‘good’ and the ‘P’ for ‘practice,’ the ‘x’ in the middle is replaced by the respective abbreviation for the specific application area.
Similar guidelines for the pharmaceutical sector have been prepared, for example, by the European Medicines Agency (EMA), the US Food and Drug Administration (FDA), and, on a global scale, by the International Council for Harmonization of Technical Requirements for Pharmaceuticals for Human Use (ICH).
Good Manufacturing Practice (GMP) is a guideline for quality assurance in the production of pharmaceuticals. Similar guidelines apply to the manufacturing of medical devices, cosmetics, and food. The basic principles of a Quality Management System are typically implemented in the chemical industry, even if not GxP regulated.
BPM methods & tools as a success story
Process management has contributed to substantial improvements over the past two decades with its methods and tools in many areas.
As examples, to mention projects for introducing SAP software, ISO 9001 based management systems, and risk management.
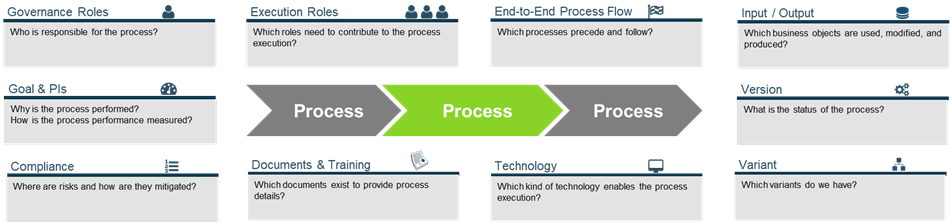

Limited success in the GxP-regulated industry
In contrast to the success mentioned above, BPM in the GxP-regulated industry is limited. It is true that, e.g., in IT projects (especially in the SAP context) or Operational Excellence initiatives, meaningful contributions to the company’s success have been made. A rapidly growing area is controlling in-house services through processes if they are not relevant to GxP. Nevertheless, it can be said that process management does not play a role here in the core processes.
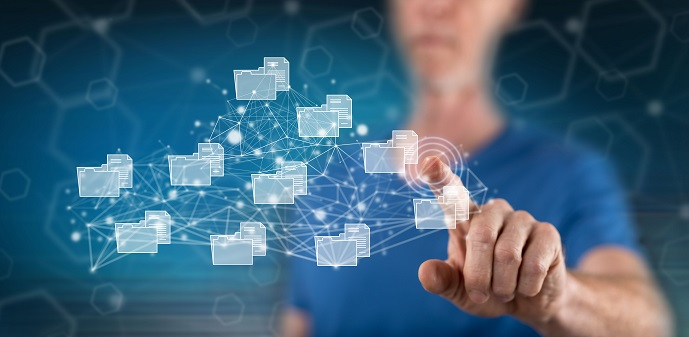
Elements of a GxP-compliant Quality Management System (QMS)
To understand the initial situation, it is necessary to note what constitutes a GxP compliant QMS:
- Management of regulations
- Qualification / Validation
- Deviation management
- Change management
- Training of employees
- Risk management
- Internal audits
As topics 2 – 7 above are based on and derived from regulations management, it becomes evident that a GxP-based QMS is driven by regulations and thus by historically grown documents. Of course, various document types have to be distinguished in detail, e.g., Standard Operating Procedures (SOPs), Operative Instructions, and Training.
At least in the SOPs, even if unstructured (i.e. ‘free text’), individual elements can be identified that also apply to processes:
- Governance Roles
- Execution roles
- Activities (tasks, events, gateways)
- Terms (definitions)
- References to external regulations
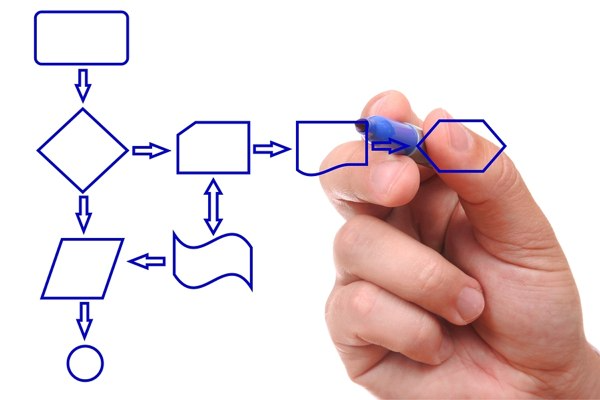
In other words, a procedure describes a process. But if all the core processes are already described in the format of documents, what can process management do to improve them?

The actual state and its disadvantages
In their own way, documents have already had a long history of transformation.
In addition to advantages (a comprehensive system that works for the intended purpose = is compliant), however, weaknesses and limitations are becoming more and more apparent in everyday life: substantial effort is recorded as ‘compliance cost.’ This consists of:
- Efforts to create documents
- Efforts to modify documents – mass change is not possible because of unstructured data
- Redundancies and contradictions between documents, e.g., roles and terms, are defined in many places and differently
- It is time-consuming to find relevant information in documents
In addition to these quantitative disadvantages, employees also complain of two qualitative aspects that seem to be contradictive: On the one hand, documents are far too untargeted (I get a lot of information that does not affect me / my role at all). On the other hand, the ‘big picture’ is missing. The focus is on the individual document, whereas purpose, the end-to-end process, or the customer benefit are not visible.
Overall, the QMS is a grown landscape of independent local regulations with various redundancies and high overall costs.
Objectives and Opportunities of Digitization
First of all, it has to be considered, that thousands of documents, and in very large companies over all sites, even hundreds of thousands, are concerned. On the other hand, the time pressure is limited if we assume that there is a working QMS.
The goal is to build a fully digital solution. In practice, the following advantages have been demonstrated:
- The principle of reuse of master data (established in financial and commodity processes, e.g., in SAP since the 1990s) helps to reduce duplication of work
- Simple mass changes: since it is clear what information is used where mass changes can be made
- The user experience should meet or go even beyond current standards (see ISO 13407 “user-oriented design of interactive systems”). This leads to greater efficiency and acceptance among the recipients of the information.
- A primarily graphical design follows the insight that visual information processing in humans is incredibly efficient and that a lot of information can be accommodated in a small space
- Mobile and media capabilities: to have everything available on your handheld is a necessity, whereas incorporation of videos on activities would be at your highest level of maturity.
- Personalization: Users see the overall context but can filter very precisely if necessary, e.g., according to their execution role: what is relevant for me?
Steps to a transformation
- A Process Map ensures that, on the one hand, all topics are recorded (completeness), but on the other hand, there are no overlaps. Comparing the existing procedures will quickly show that the transformation starts from a ‘many to many’ state. This means that there is relevant content for a process in several procedures. Conversely, however, a procedure usually also contains information for multiple processes.
- In addition, as mentioned above, there is ‘overarching’ information with master data character, e.g., governance roles, execution roles, terms. These are created only once in a digital solution and can be referenced from there.
- Select next level IT platform: there are now innovative tools on the market that manage all process and SOP content as information while still enforcing the pharmaceutical compliance requirements like change management, impact assessment, endorsement or approval, and governance workflows, including FDA 21 CFR part 11 compliant digital signatures.
Digital Transformation of QMS: Example of a Roadmap
Why Choose Interfacing?
With over two decades of AI, Quality, Process, and Compliance software expertise, Interfacing continues to be a leader in the industry. To-date, it has served over 500+ world-class enterprises and management consulting firms from all industries and sectors. We continue to provide digital, cloud & AI solutions that enable organizations to enhance, control and streamline their processes while easing the burden of regulatory compliance and quality management programs.
To explore further or discuss how Interfacing can assist your organization, please complete the form below.

Documentation: Driving Transformation, Governance and Control
• Gain real-time, comprehensive insights into your operations.
• Improve governance, efficiency, and compliance.
• Ensure seamless alignment with regulatory standards.

eQMS: Automating Quality & Compliance Workflows & Reporting
• Simplify quality management with automated workflows and monitoring.
• Streamline CAPA, supplier audits, training and related workflows.
• Turn documentation into actionable insights for Quality 4.0

Low-Code Rapid Application Development: Accelerating Digital Transformation
• Build custom, scalable applications swiftly
• Reducing development time and cost
• Adapt faster and stay agile in the face of
evolving customer and business needs.
AI to Transform your Business!
The AI-powered tools are designed to streamline operations, enhance compliance, and drive sustainable growth. Check out how AI can:
• Respond to employee inquiries
• Transform videos into processes
• Assess regulatory impact & process improvements
• Generate forms, processes, risks, regulations, KPIs & more
• Parse regulatory standards into requirements
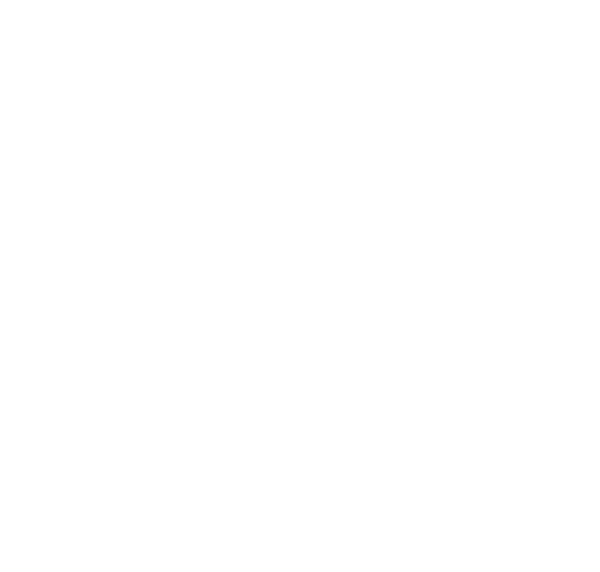
Request Free Demo
Document, analyze, improve, digitize and monitor your business processes, risks, regulatory requirements and performance indicators within Interfacing’s Digital Twin integrated management system the Enterprise Process Center®!
Trusted by Customers Worldwide!
More than 400+ world-class enterprises and management consulting firms
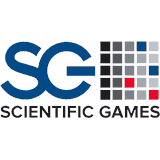
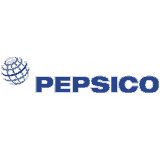
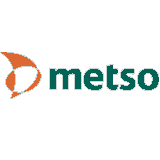
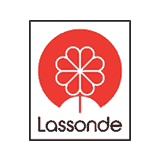
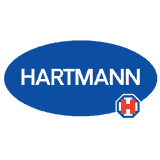
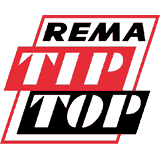
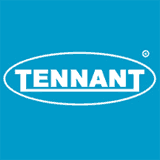
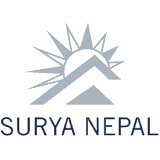
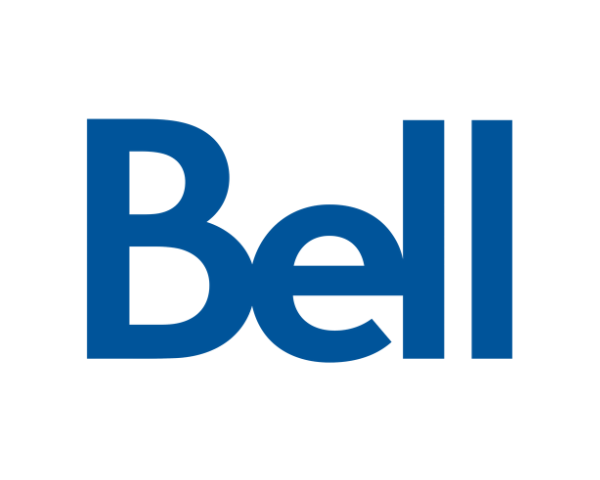
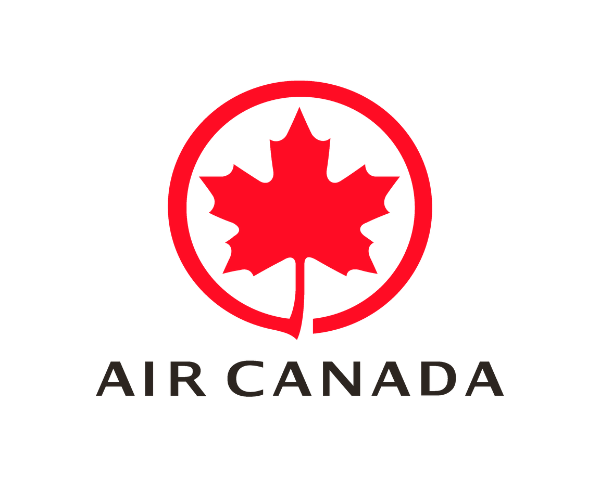
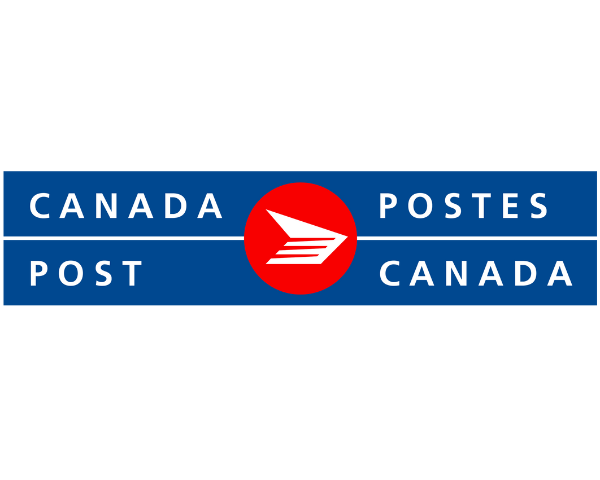
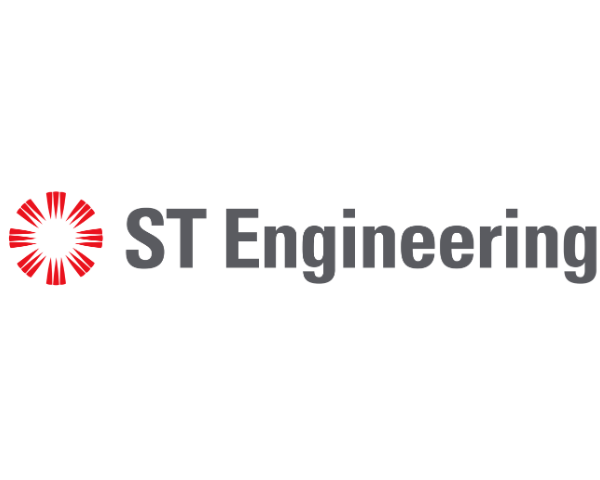

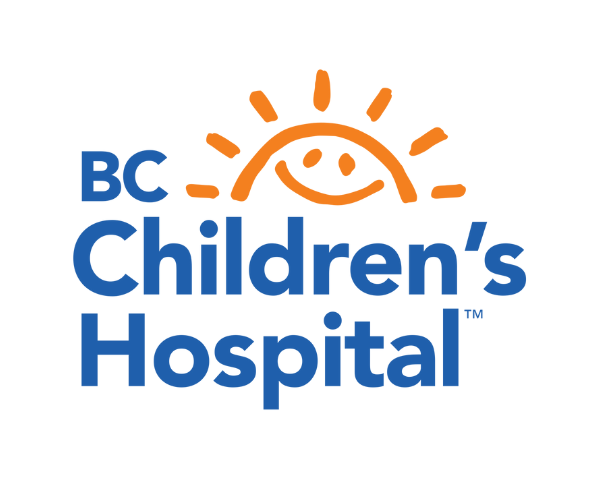
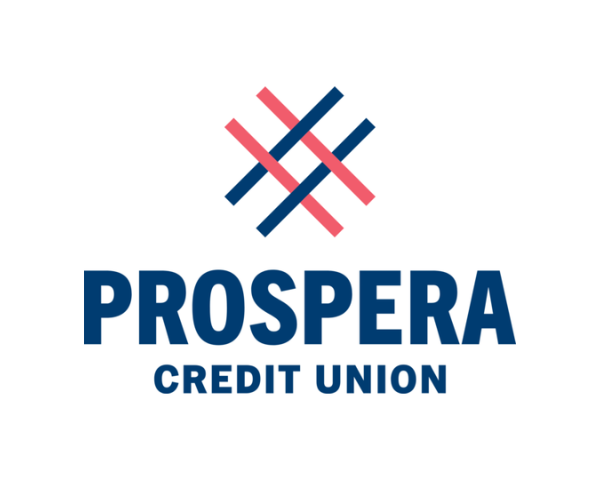
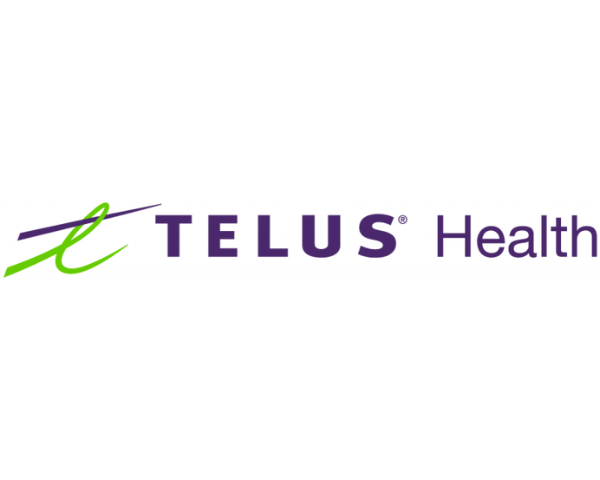
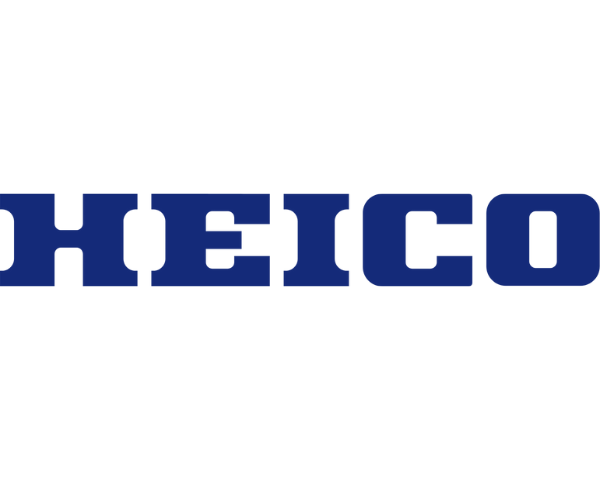
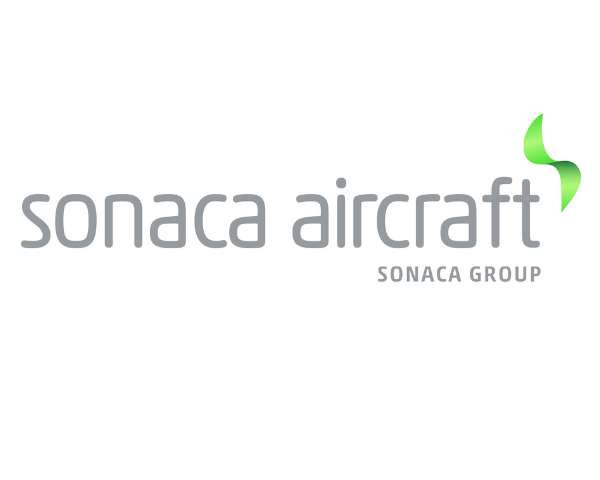
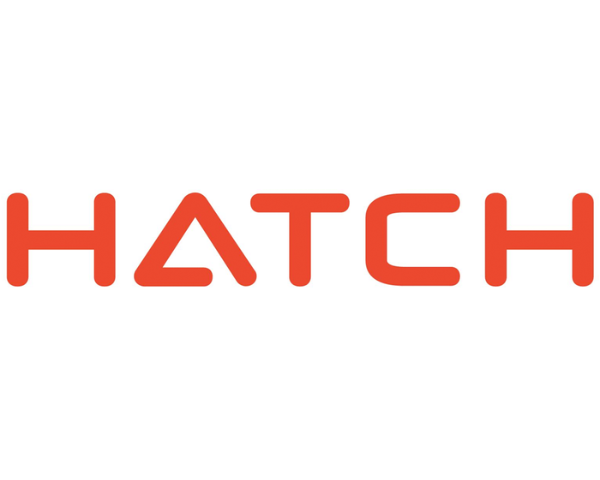
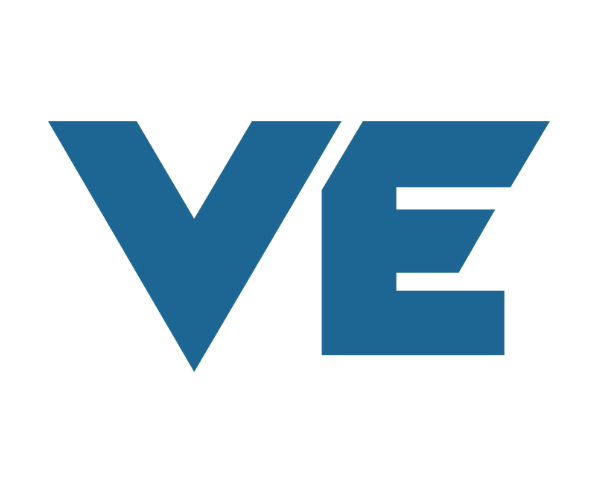
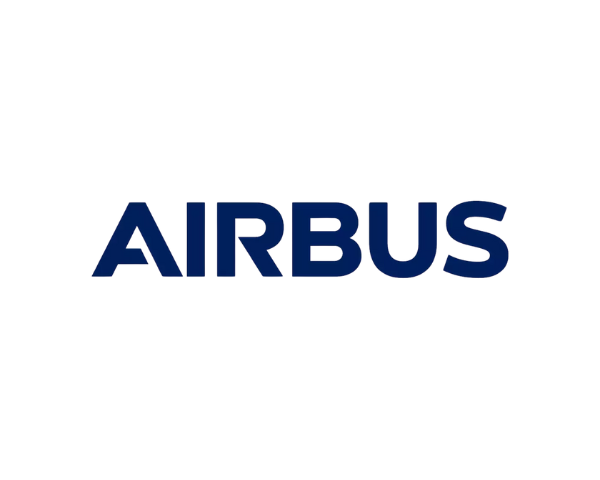
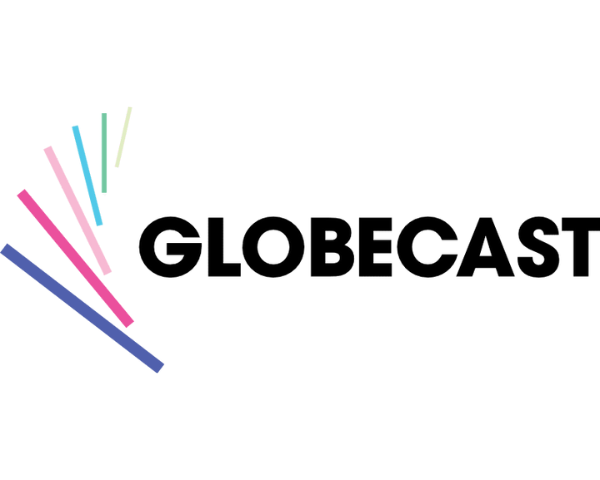
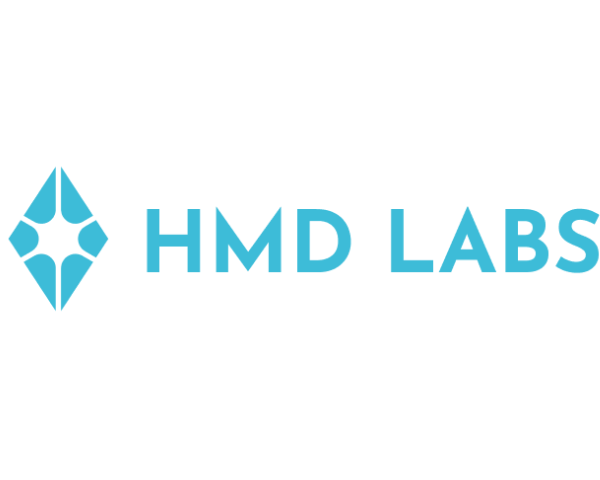
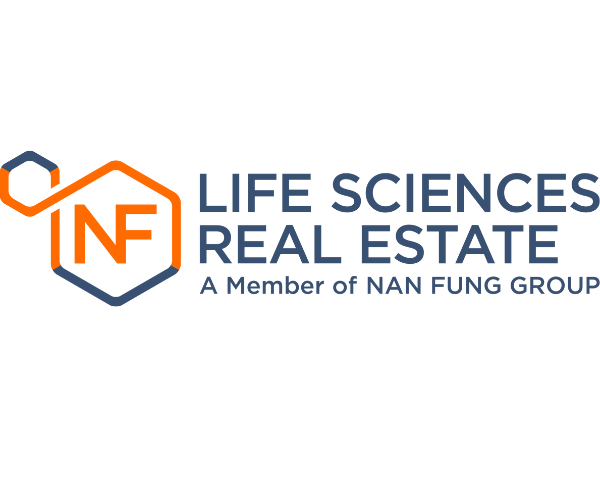
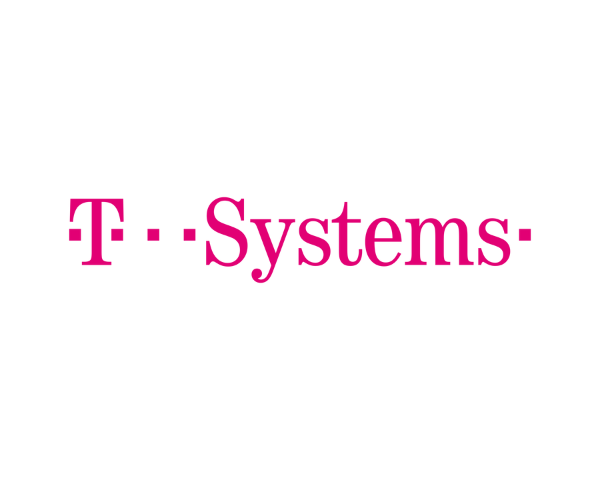
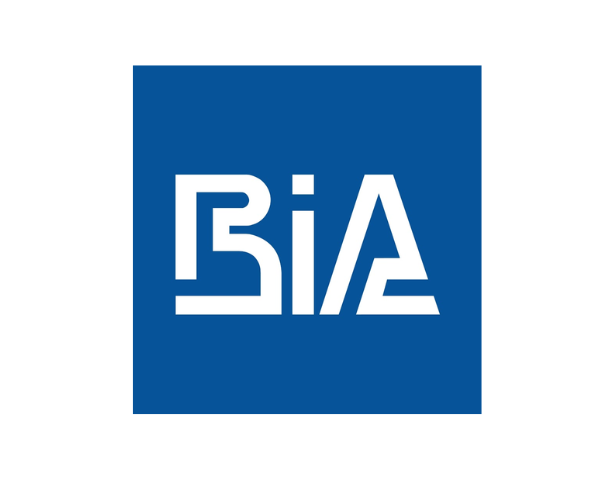
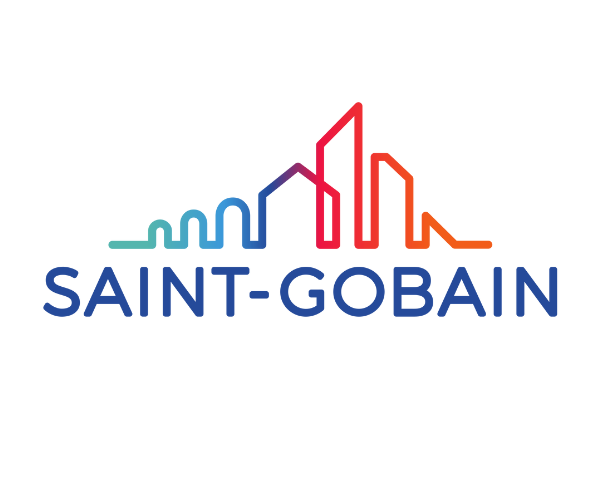
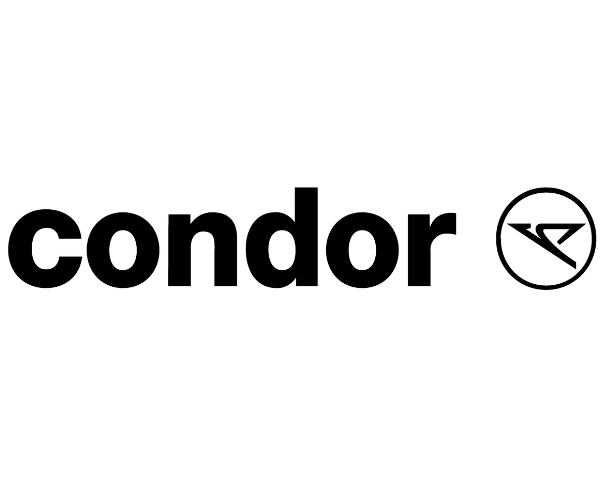
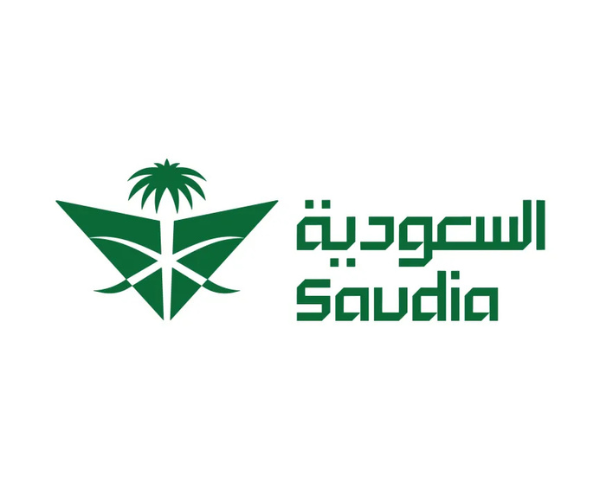
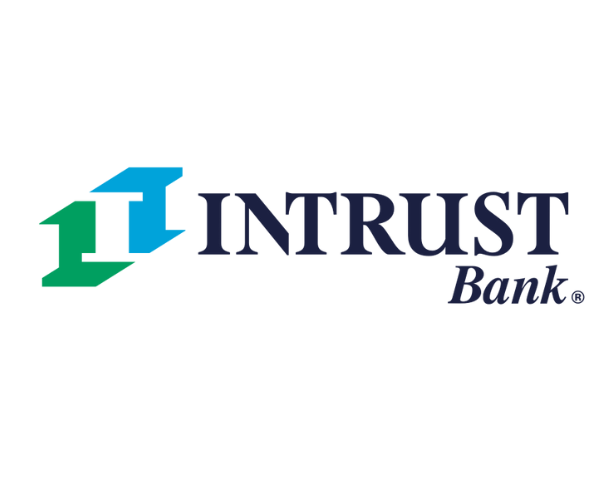
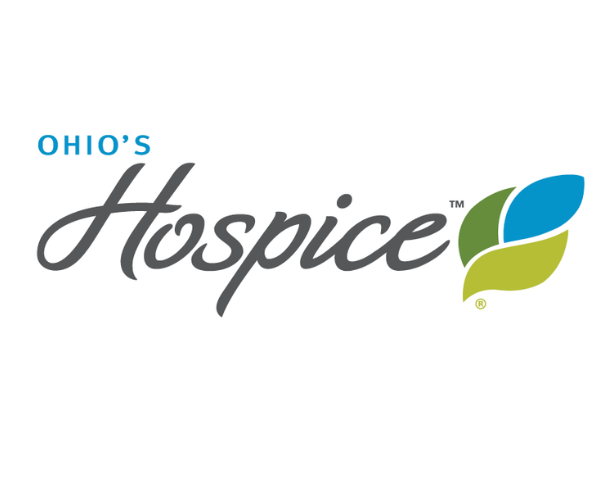
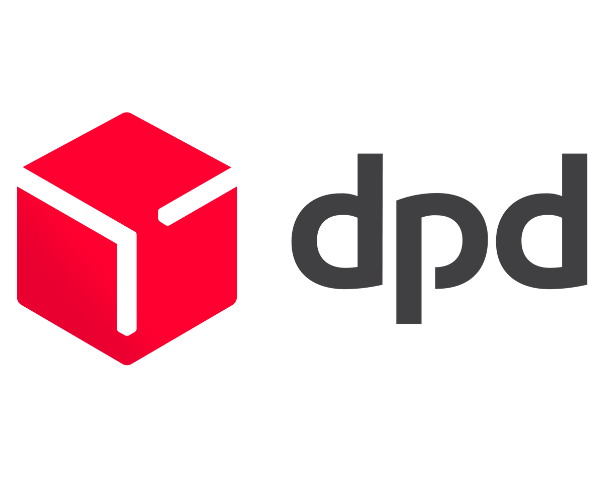
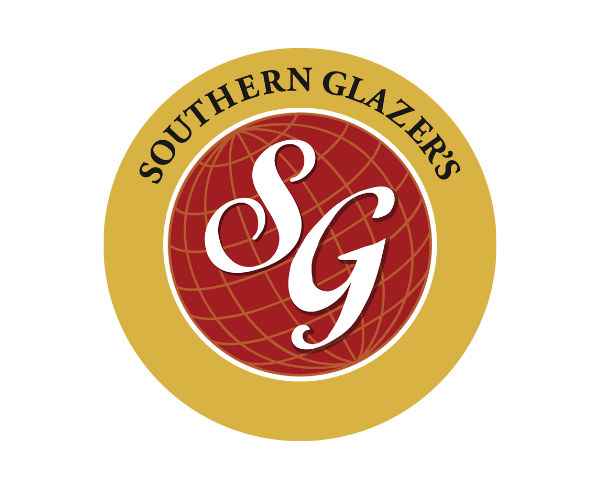
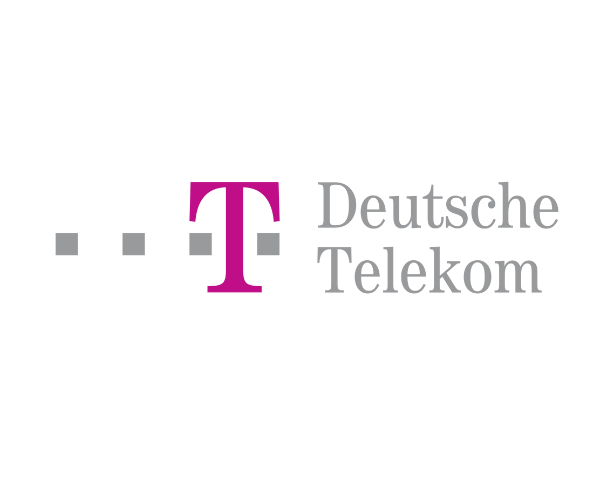
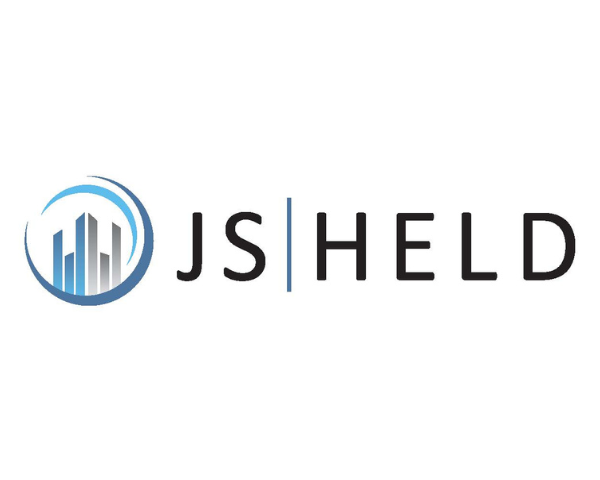
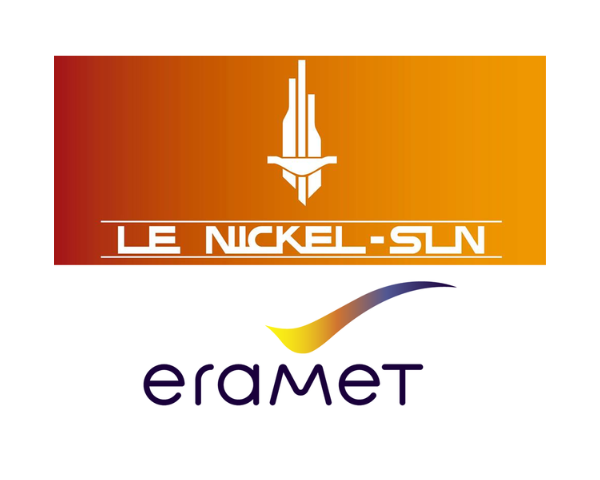
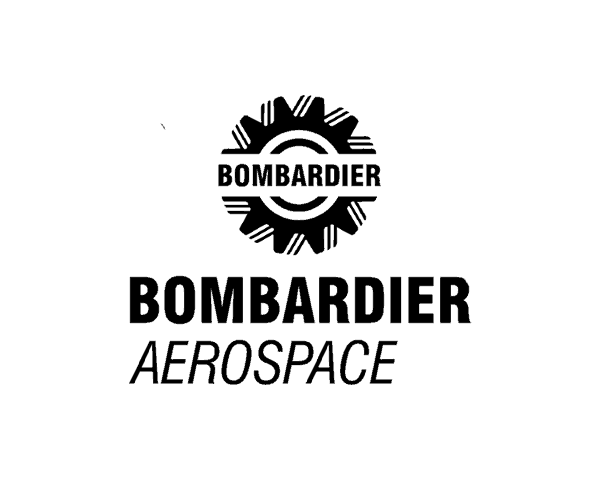


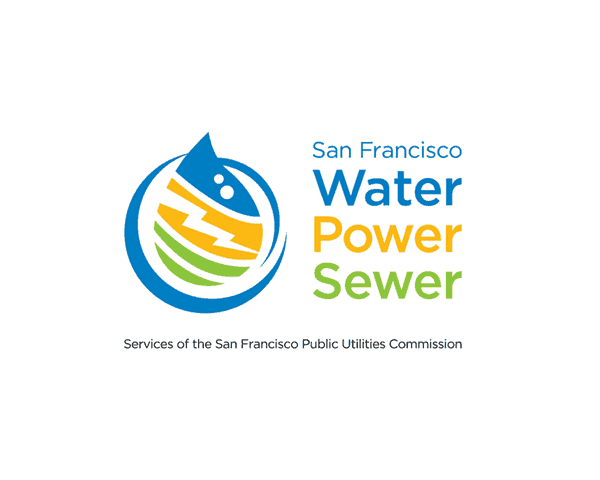
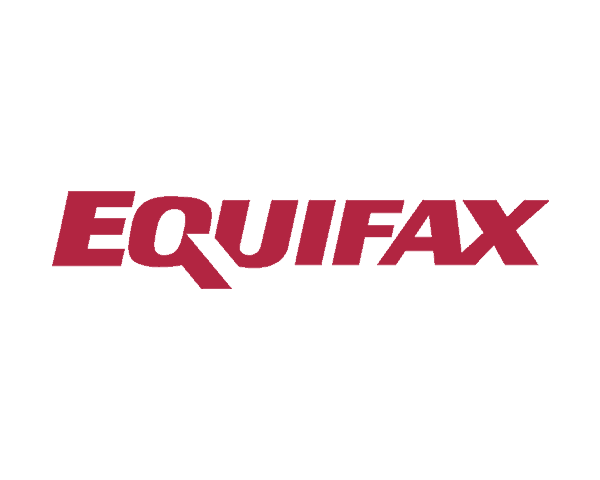
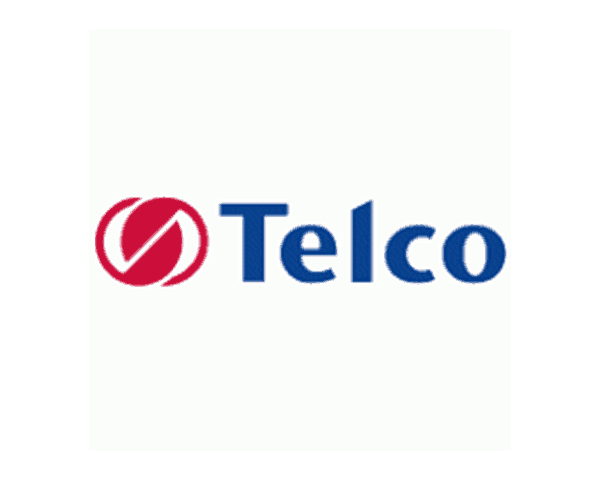
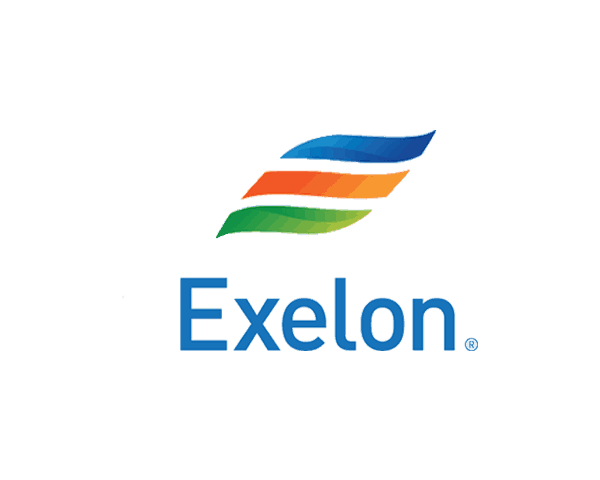
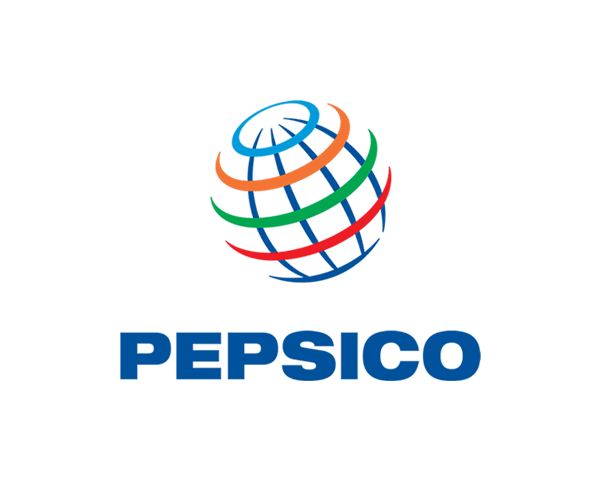
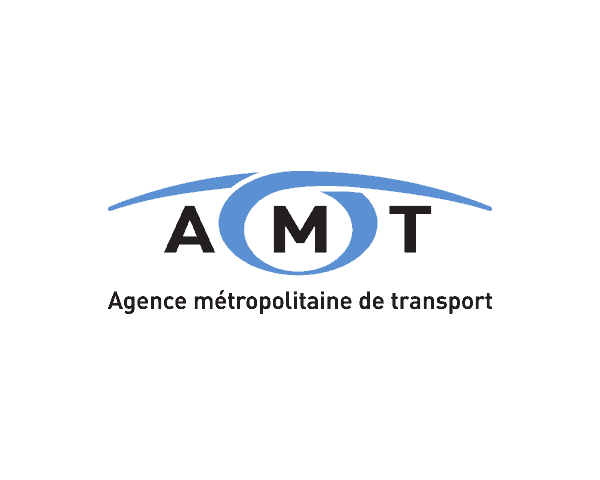
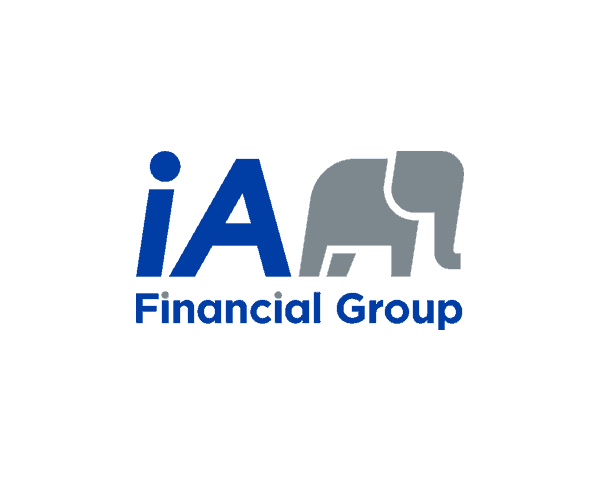
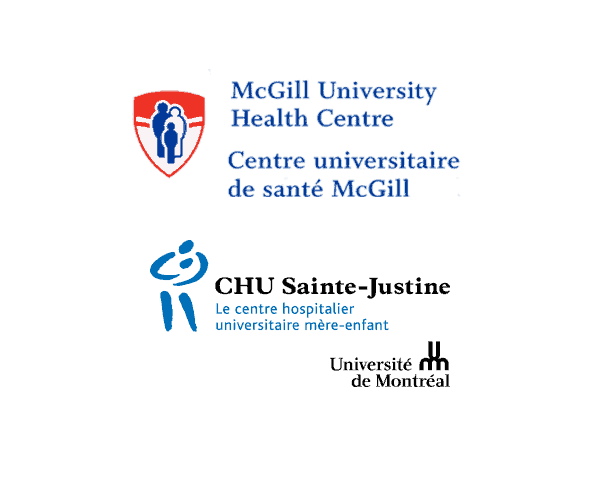
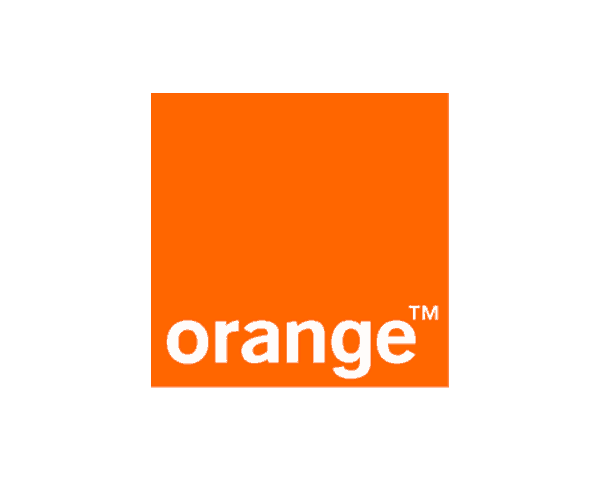
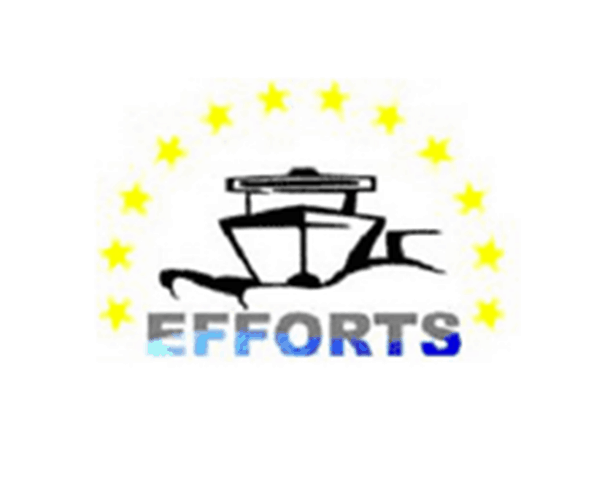
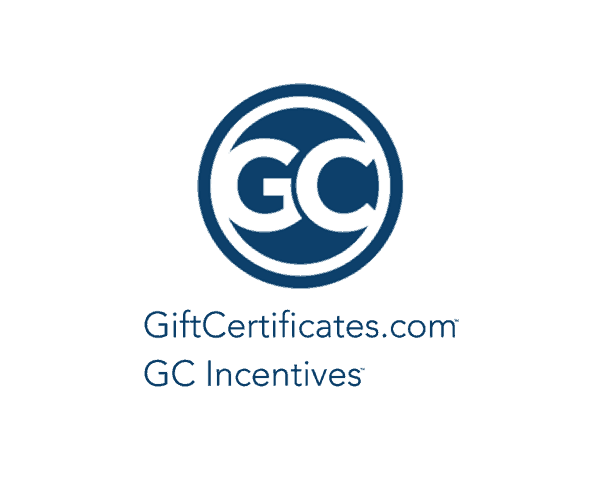
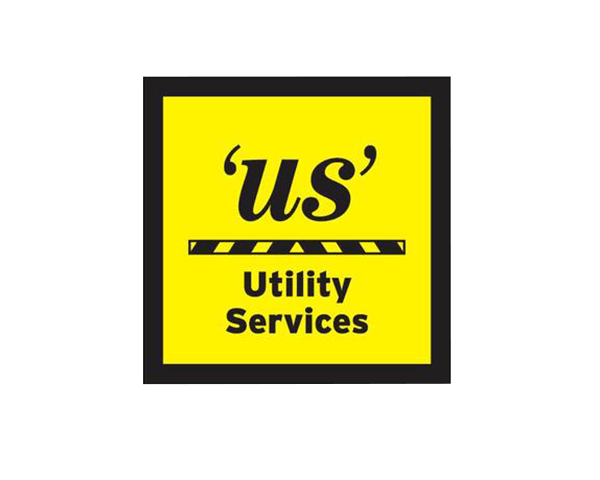